In digital inkjet printing, the high-speed jet of ink is a decisive factor that determines whether the textile matrix can be successfully printed.
The ink must be formulated carefully so that the physical and chemical characteristics of the ink used meet the best process parameters, ensuring an effective printing operation and obtaining a satisfactory print pattern on the surface of the fabric.
The ink formulation for high-speed digital ink jet printing requires a balanced performance to ensure the best stability of the ink prior to application, allowing high-speed jets to operate without obstacles. When the ink hits the surface of the fabric, the ink droplets should have satisfactory wetting/absorbing properties. This can be controlled during prepress pretreatment of the fabric.
Obviously, ink formulations must be suitable for specific types of ink jet printing systems, whether based on Piezoelectric Drop On Demand (DOD) or thermal spraying or based on continuous inkjet technology. About 80% of digital ink jet printers used for textile crystals use piezoelectric drop-on-demand and the rest are mainly thermal jets.
Therefore, the ink in the ink formulation must be matched with the printing machine to give the textile a satisfactory performance (such as color, fastness), to efficiently print at the lowest cost, and to provide corresponding services for possible technical problems.
1 ink performance and requirements
The preparation of high-speed digital inkjet printing inks is different from conventional dyeing and printing of conventional dyes or coatings. Even if the same dyes are used, their preparation is not the same. Inkjet printing inks are high-tech products and play an important role in the forefront of textile printing technology. At present, certain chemical companies pay considerable attention to the research and development of inks for digital inkjet printing of textile materials. This is a field full of creativity. It is a specialized skill in the application of high-tech chemicals to textiles. It provides printing workers with ink formulations to achieve the right balance between the technical requirements of ink and the quality of printing.
2 Dyestuffs for digital printing
Traditional textile printing pastes may contain 30%-50% of dyes, the rest are diluents and dispersants, etc., while the dyes and coatings used in digital inkjet printing inks must have high purity and are ground to a finely particulate state. Degree <1μm. The color development properties of dye chromophores must be very strong because the dye concentration in a typical commercial printing ink is only about 10%. In the piezoelectric ink-jet printing, the maximum amount of ink applied in a single channel is only about 20g/m2, and the dye remaining on the fabric is 2g/m2, which is compared with the conventional screen printing with a dyeing rate of 100g/m2. The dye left on the fabric is more than five times that of the former. In this way, inkjet printing typically applies multiple inks in several passes to increase the color depth of the printed pattern. The higher the color strength of the dye is, the easier it is to print darker colors. However, there is still the problem of color depth for ink jet printing of textile crystals.
Although some manufacturers use printing heads derived from industrial digital printing machines, most ink jet printing machines still use printing heads originally designed for the printing industry because it may be more reliable under the textile printing operating conditions. Piezoelectric print heads can take into account the relationship between resolution and speed, and provide a great range of applications for the development of new inks. The use of CMYK (cyan, magenta, yellow, black) color gamuts is not sufficient for digital inkjet printing of textile crystals, and six colors may be used, but eight colors are generally used more. For example, in the DuPont 700 series of inks, CMYK four colors are added to P700 coating ink, A 700 acid dye ink, R700 reactive dye ink, and D 700 disperse dye ink. DuPontP 700 series coating inks have increased red and blue, A700 series has added red, green, blue, orange, fluorescent yellow and fluorescent red, R700 series ink has light magenta, light blue, blue and orange, D700 series The ink has increased red and blue. DuPont 500 series inks can be used for low-viscosity piezoelectric printing technology, CMYK four-color and light cyan, light magenta, red, green and purple; DuPont 500 series water-based inks, can be used for high-viscosity piezoelectric printing head, using CMYK four-color and light cyan, light magenta, red, green, blue and orange.
At present, acid dyes can be used for inkjet printing, can be printed sportswear, swimwear, underwear, flags and accessories; reactive dyes can be used for casual clothes and underwear; and disperse dyes account for about 50% of the digital textile printing market, Most of them are used as transfer printing inks for the printing of clothing, bunting, automotive and furniture decorative fabrics.
3 Physical and Chemical Properties of Ink
Ink for digital inkjet printing must carefully describe the applicable print head technology. Ink properties, such as viscosity, electrical conductivity, surface tension, chemical stability, physical stability, flowability, filterability, pH, and non-foaming properties are all very important. Ink manufacturers design ink properties and produce high-performance inks. The viscosity of the ink is of primary importance because the spray action is primarily determined by the viscosity parameters. The reliability of inkjet printing has several important influencing factors, including drop volume, jet speed and linearity, and pot life (storage life). If the dyes used remain in the fixed ink container, these dyes must not crystallize, coagulate or clump, nor precipitate or delaminate. If the medium evaporates or foams, air traps or contaminates the equipment, it may cause problems.
Ink formulations are complex and each ink has its own special properties in addition to its common composition. Demineralized water is used to prevent the interaction between metal cations and dye anions in the water, and to ensure that the conductivity value of the ink is consistent. By adding a small amount of surfactant to control the wetting/permeating properties of the ink, the water-soluble solvent imparts moisture absorption to control the viscosity. The pH stability during storage is important, using a buffer solution to control the pH within a limited range. The use of insecticides prevents the growth of mold and bacteria in the ink and in the print head. In the early stages of ink-jet printing, people have not yet known that it is due to the growth of moulds/bacteria that cause nozzle clogging.
The development of insoluble pigment-based inks and small amounts of water-soluble disperse dye-based inks has brought significant challenges to ink formulations. The production of finely divided submicron disperse dye inks is particularly difficult, but the stability of the ink is sufficient, and the stable life is extremely long. The performance of the ink must be tested under actual ink jet printing conditions to determine the fluidity of the ink. Ink crystallization may cause nozzle clogging, so crystal formation should be prevented. In addition, the miscibility of different dyes must be satisfactory when they are mixed at some point on the fabric surface. This is the difference between digital printing and traditional screen printing. Screen printing dyes are first pre-mixed and then applied directly to the fabric; ink jet printing is directly sprayed onto the surface of the fabric through several sets of ink droplets to produce the final color effect.
Coating (or pigment) based inks must use adhesives. In traditional screen printing, adhesives are added to printing pastes, and digital printing has three methods of applying adhesives:
(1) In the ink dispersion formula;
(2) through a separate nozzle system (transmission channel);
(3) Apply adhesive after inkjet printing.
According to the drop-on-demand printhead technology, different requirements are placed on paint (or pigment) inks. BASF has developed two coating inks that do not contain a textile binder. Helizarin P inks are suitable for low-viscosity piezo printing heads; Helizarin H inks are suitable for hot bubble jet drop-on-demand printing heads with a resolution of 600 dpi. Helizarin EVOPl00 coating ink developed by BASF is a new low-viscosity (<5mPa·s), soft coating ink, which can improve the printing quality, giving the product richer, more vivid colors and finer print profiles. The ink uses a new, versatile polymeric dispersant to disperse and stabilize coatings, impart high color strength to fabrics, improve print silhouette clarity, and improve rubbing fastness, wash fastness, and vividness.
Obviously, the innovation of ink formulation chemicals in digital printing can produce significant technical and economical effects. However, depending on the color fastness in a particular color gamut, there is still a need to develop chromophores in the dye structure to solve the problem of color fastness in certain color gamut ranges. Dyestuff manufacturers are continuing to improve ink technology to solve specific technical problems, and should be ahead of the consideration of ink requirements for the next generation of print heads.
(Source: China Washing & Dyeing Industry Information Center)
Orient IRIS-F is a new green printing plate which is suitble for thermal CTP setters.The plates deliver the print capabilities and productivity of mainstream plates,without the processing and chemistry.So you can reduce the cost and environmental impact and be more competitive at the same time.Processless Plate is a good product,too.It is kind of green and special printing plate suitable for thermal CTP platesetters. There is no need of any processing steps before mounting exposed plates on press. And it also can be put on press after water wash.
Characteristics:
1.Negative non-ablation photosensitive system
2.Compatible with the dominant devices in the market
3.Can be printed directly on the machine without any processing steps after scanning by thermal CTP platesetter
4.Good dot reproduction, stable performance, wide processing latitude
5.Long stability of latent image, can be stored at least a week after plate-making
6.High quality aluminum substrate, professional coating formulation
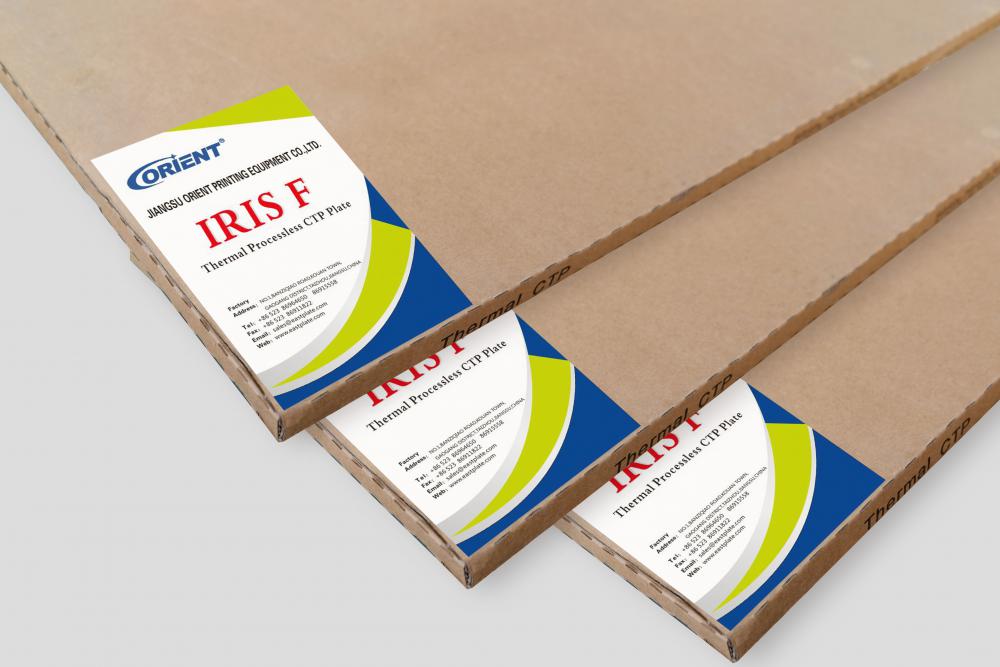
Negative Processless Plate,Processless Negative Thermal Plate,Processless Negative CTP Plate,Offset Plate,Negative Plate,Presensitized Plate,Processless Plate
Jiangsu Orient Printing Equipment Co.,Ltd , http://www.eastplate-iris.com